Expert Solutions for Pump Systems
Enhance efficiency and reduce costs in your processes.
Increase MTBF
Maximize uptime and efficiency in operations.
Streamline your chemical processes effectively.
Optimize pulp and paper systems seamlessly.
Cost Reduction
Process Optimization
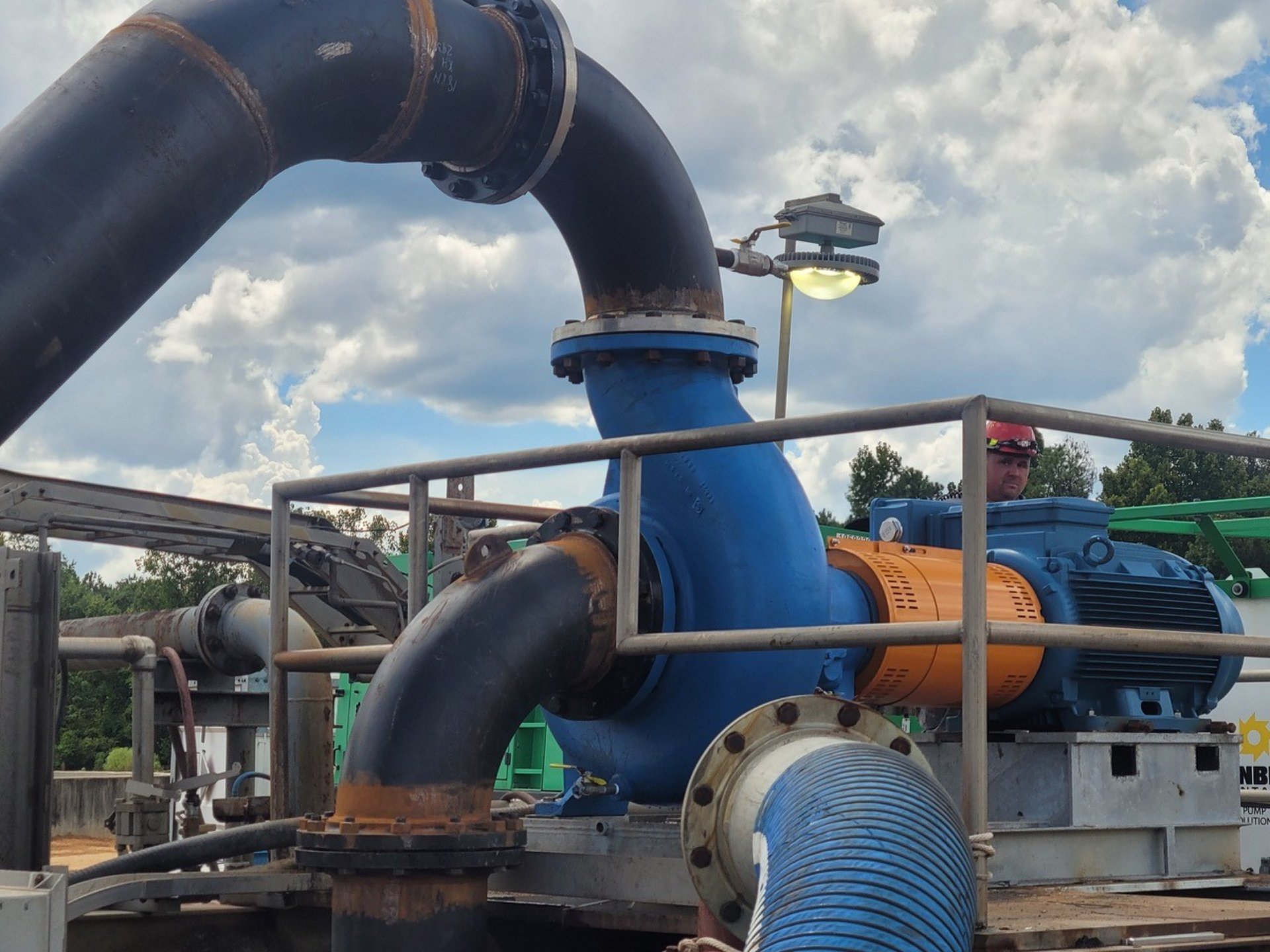
Your Trusted Pump Experts
At Pump-Man Consulting, we specialize in providing expert solutions for pumps and systems in the pulp and paper and chemical process industries, ensuring efficiency and cost-effectiveness for your operations.
Experts you know and trust
Expert Pump Solutions
Enhancing efficiency and reducing costs in pulp and paper and chemical process industries with expertise.
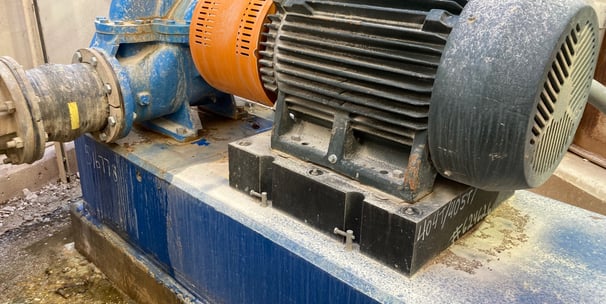
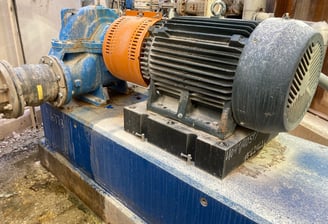
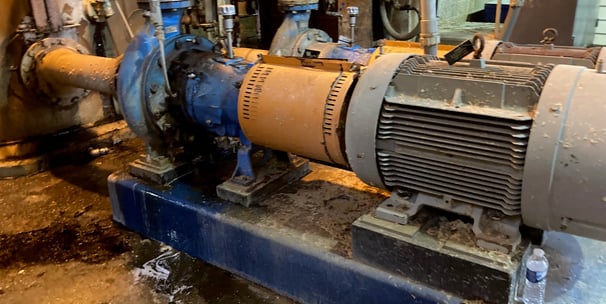
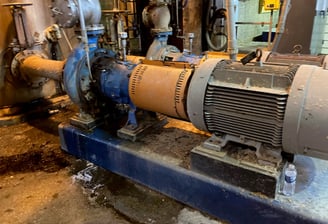
Cost Reduction
We help you reduce operational costs while increasing the reliability of your pumping systems effectively.
System Optimization
Our experts optimize your processes to ensure smooth operations and improved mean time between failures.
Case Study; A major Kraft mill in the southeast USA.
Large double suction pump was breaking shafts 3+ times per year. This had been going on for as long as anyone could remember. Pump was supplying white water to Save all and to dry end pulper and couch pit during machine breaks. Operators complained they never got enough water from this pump and it would trip the motor if CV was opened beyond 20%.
We quickly determined that the OEM documents showed an operating speed of 1180 RPM but an impeller below minimum diameter. An investigation of the piping and control system showed minimal friction loss to any of the users.
We made recommendations to install 880 RPM motor and a 19.5" impeller. In doing these things the pump was able to make the required flow and TDH was reduced. The pump had the flexibility to operate reliably and meet operating conditions. Shaft breakage has ended
Estimated cost of this service; $6000
Maintenance savings to the mill; $100,000 yr
Meeting operating requirements; PRICELESS
John Doe
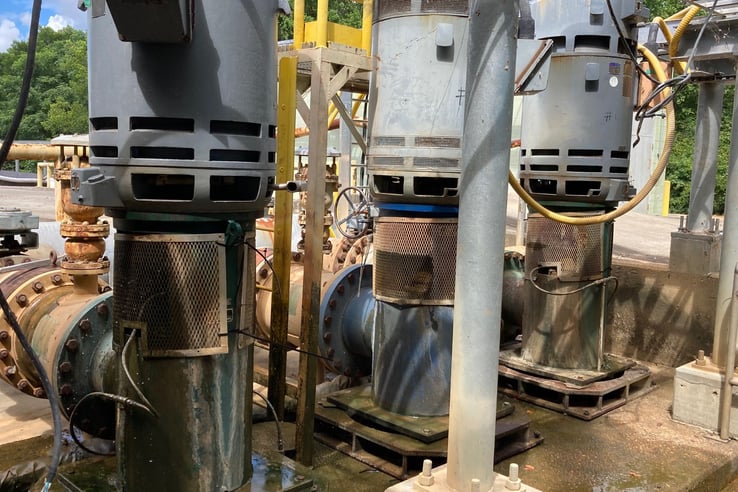

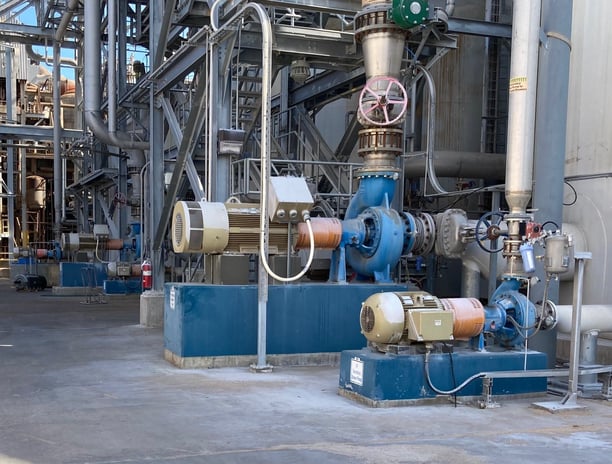
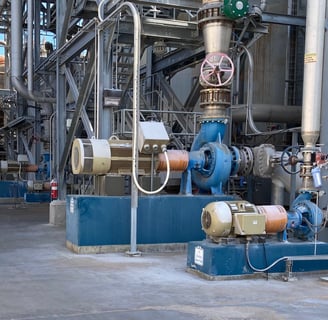
★★★★★
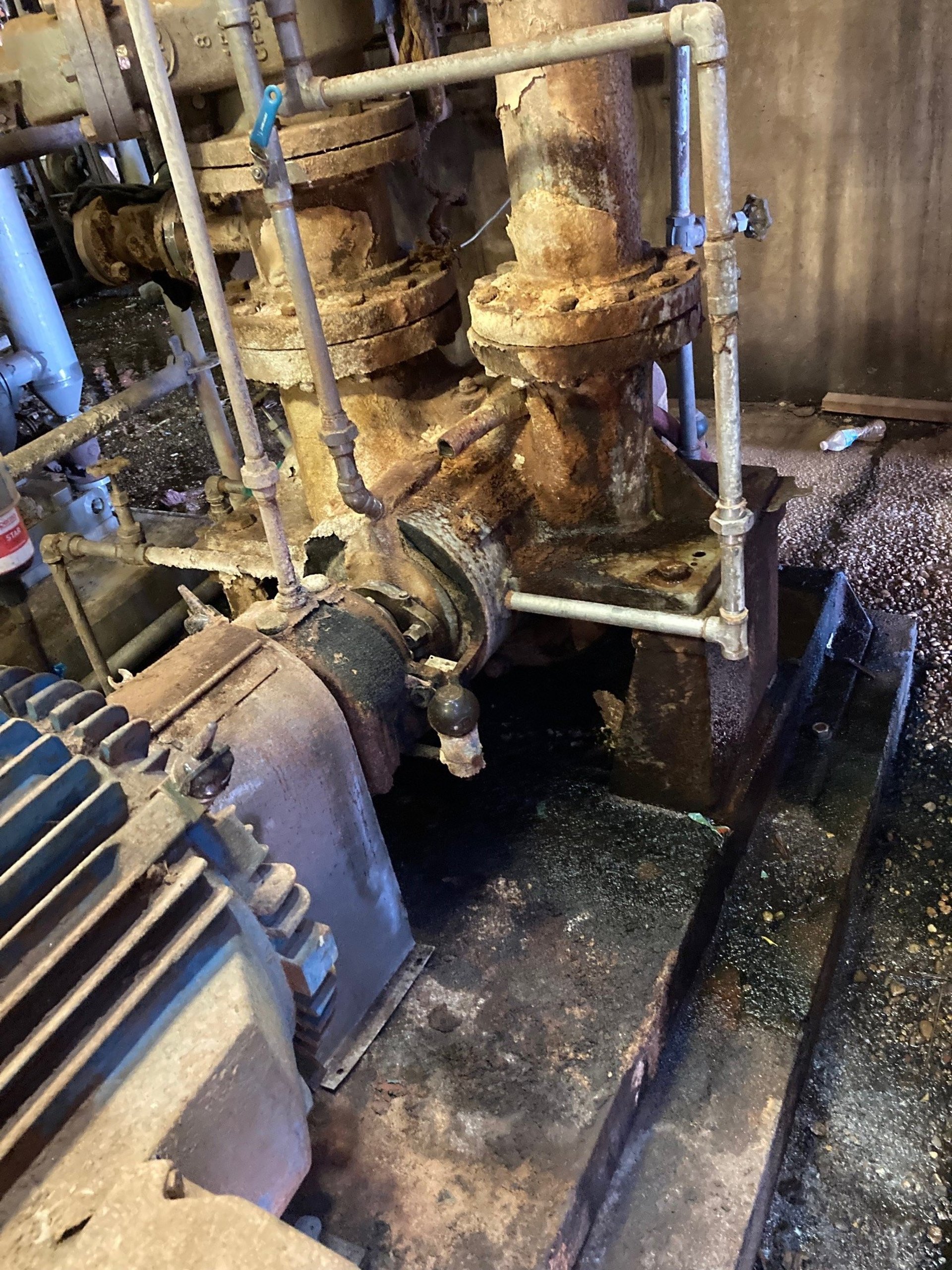
Pump Solutions
Expertise in optimizing pumps for various industrial processes.
Case Study
A major Pulp producer in Southeastern USA was losing mechanical seals on chemical mixers within weeks of installation
. We studied the problem and based on the seal water system using seal pots, were able to determine the seals had not failed but were leaking from the gasket connection to the stuffing box.
Customer had been replaced several seals that had not actually failed.
We advised ways to check for seal failure and made recommendation to torque seals properly.
Estimated cost; $1200
Savings; $25,000 plus downtime
Case Study;
Major linerboard producer in Southeast USA was wrecking HP shower pumps weekly. When a pump wrecked there was no spare shower pump. Supplying both machines with one pump would cause motor overload.
Maintenance brought us the problem. We interviewed operations personnel as well as the machine clothing suppliers.
It seemed that over the years the impeller diameters (4 stage pump) had been increased. This meant that the pump was producing about 750 psi when the machine only needed about 400 psi. The pressure was so high and the flow rate was so low that the pump would only last for 1 week to 10 days.
We convinced the mill to trim the impellers down to make the pumps non-overloading for the 400 HP motors. This allowed one pump to supply both machines without overloading the motor. It improved reliable operation to several years and reduced the power from 2x400 HP to just one motor operating and caused them to have a spare pump.
Estimated cost; $6000
Savings; $20,000 spent weekly plus $160,000 annual power cost
Enhancing performance and reducing operational costs effectively.
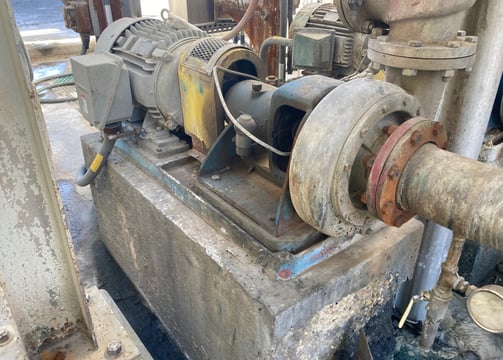
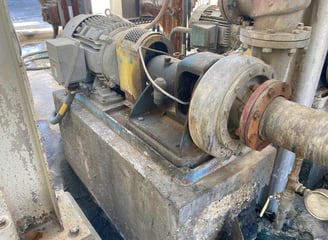
Cost Reduction
Streamlining processes to save time and resources.
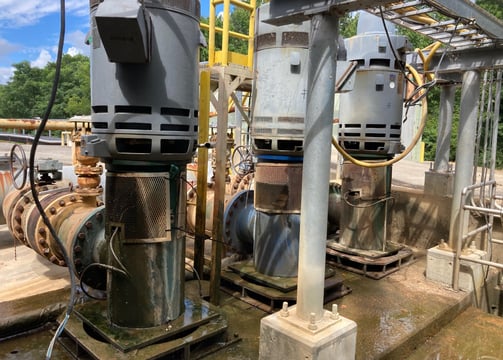
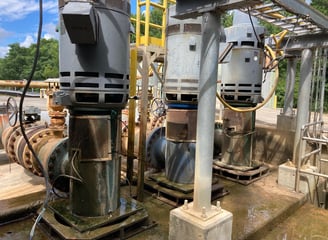
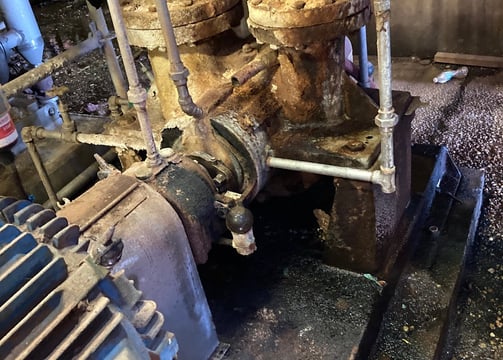
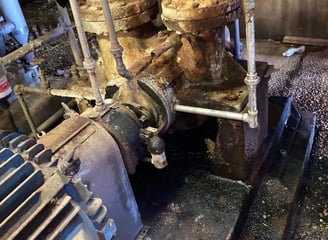
Expert Consultation
Providing specialized advice for pulp and paper industries.
System Optimization
Maximizing uptime and reliability in chemical processes.